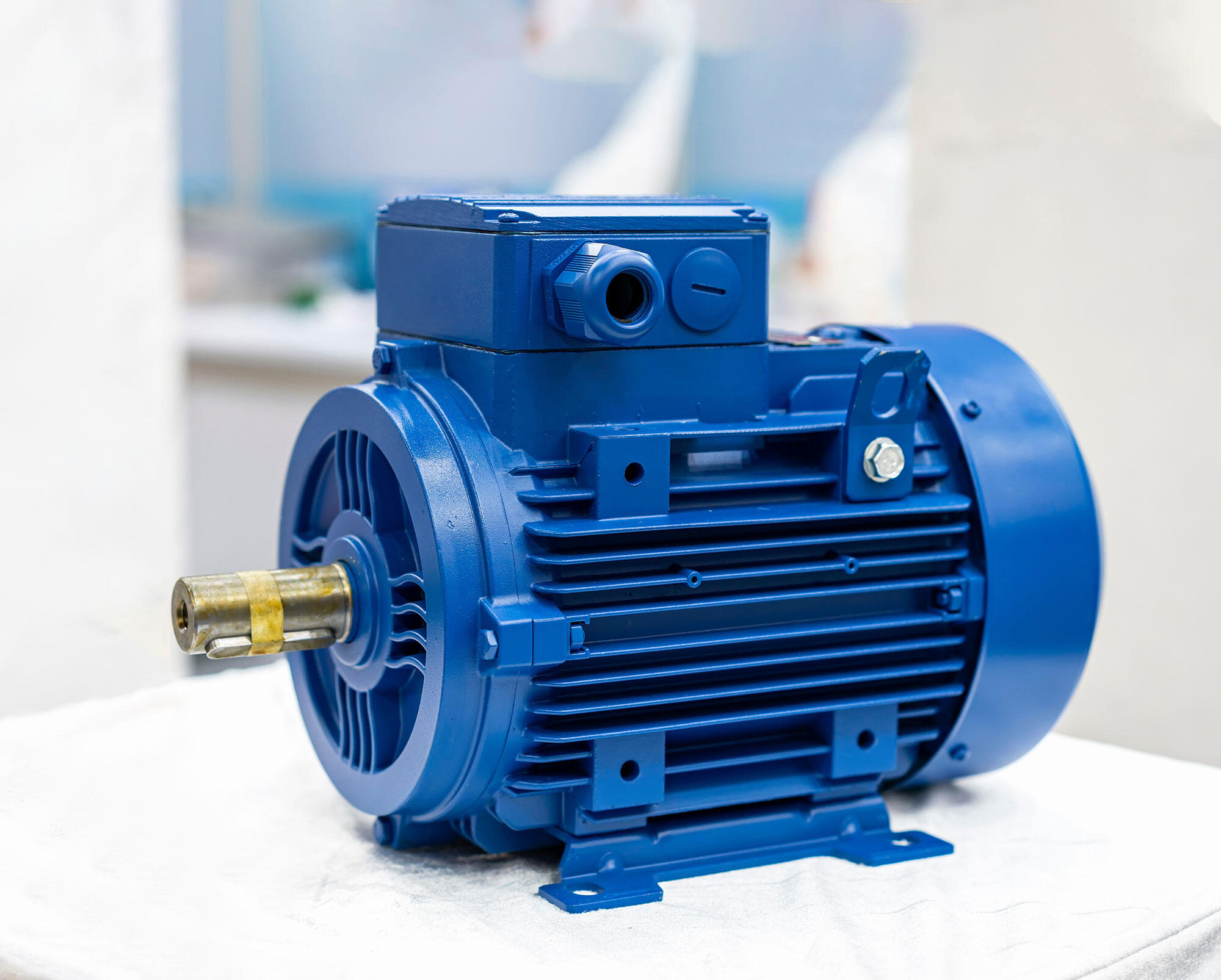
THE PRODUCT:
Electric motors convert electrical energy into mechanical energy. Typical uses for electric motors include pumps, fans, blowers, conveyors, and air compressors.
THE STANDARD:
The current standards for electric motors took effect in 2016. The standards, which were based on a joint recommendation from motor manufacturers and efficiency advocates, cover polyphase induction motors between 1 and 500 horsepower (hp), with some exceptions such as submersible or liquid-cooled electric motors.
DOE finalized new standards in 2023 based on a joint recommendation from motor manufacturers and efficiency advocates. The final rule, which requires compliance starting June 1, 2027, strengthens the existing standards for 100-250 hp induction motors and sets new standards for larger induction motors (up to 750 hp) and air-over induction motors.
KEY FACTS:
Electric motors account for nearly half of all global electricity consumption. Motor efficiency can be improved by minimizing various losses including electrical resistance losses (I2R losses), core losses, friction and windage losses, and stray load losses. These losses can be minimized in a variety of ways, including changing the rotor/conductor design, improving the quality or reducing the thickness of the electrical steel core, and utilizing improved bearings and cooling. Even greater energy savings in motor-driven systems can be achieved through the use of variable-speed controls. Reducing the speed of the motor to match the motor’s load can yield significant energy savings, particularly in variable-torque (e.g., fans, pumps) applications.
Agreements
Filings
ASAP Press Releases
Timeline
Federal | Date |
Next Review Due | 2029 |
4th Federal Standard Effective | 2027 |
4th Federal Standard Adopted | 2023 |
3rd Federal Standard Effective | 2016 |
3rd Federal Standard Adopted | 2014 |
2nd Federal Standard Effective | 2010 |
2nd Federal Standard Adopted | 2007 |
1st Federal Standard Effective | 1997 |
1st Federal Standard Adopted | 1992 |
EPACT Initial Federal Legislation Enacted | 1992 |